Daily Management is the Key to Successful Compliance Programs
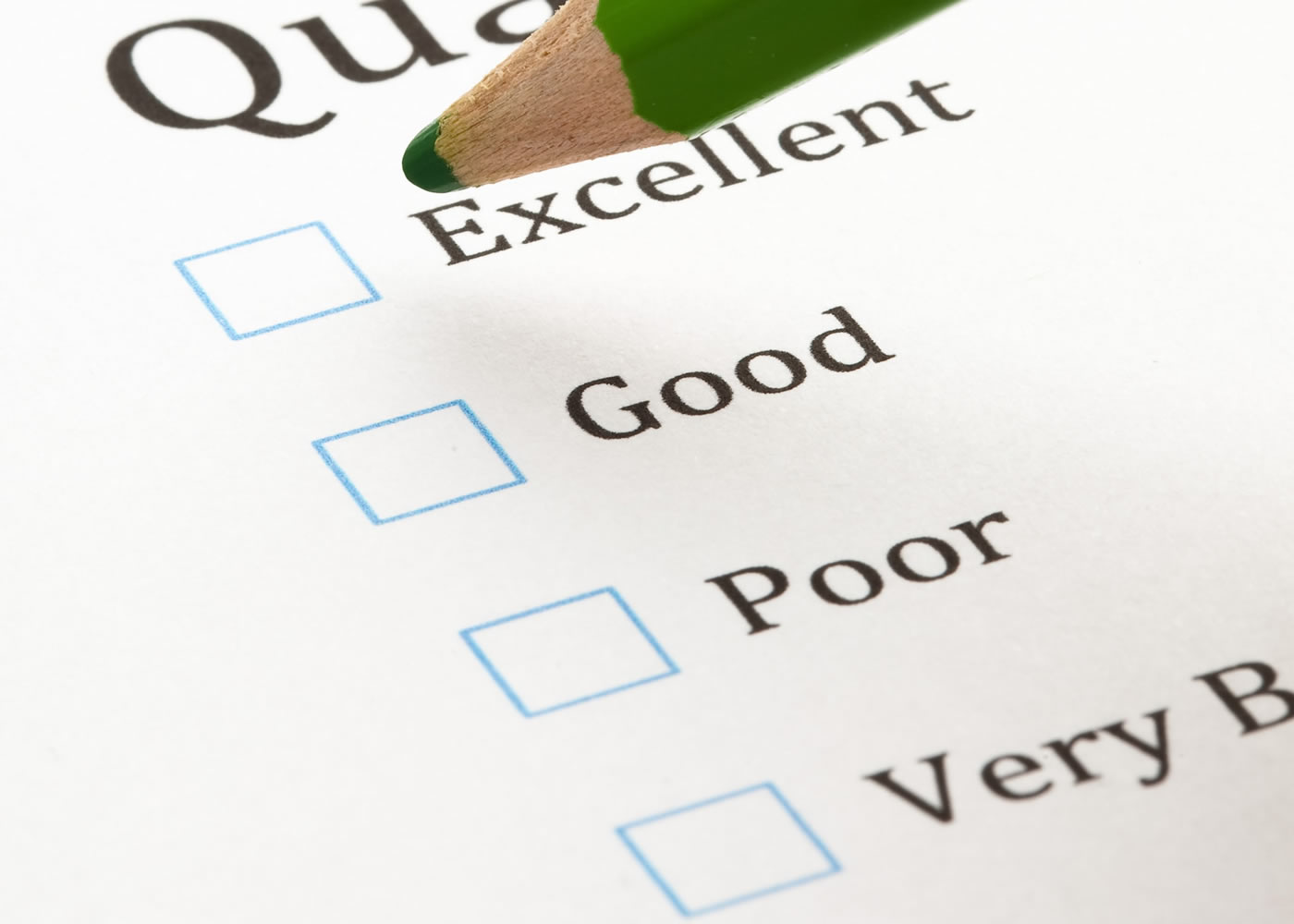
At Honeywell Aerospace, Director of Compliance Assurance Gregory Bopp says his HSE team integrates their programs into the company's operating system, which requires facility leaders to conduct daily inspections.
"Rather than waiting once a year or once every two years to demonstrate compliance through an audit, we're looking continuously on the shop floor at different levels of our operations to make sure that we're complying," he said.
This management systems approach is likewise a common practice among companies with mature EHS programs, according to recent NAEM benchmarking research among leadership companies.
Fielded in conjunction with NAEM's August 2014 "Advancing Compliance Assurance" conference, the survey of 49 corporate EHS leaders revealed that 74 percent use the ISO 14001 management system as the framework environmental compliance programs at specific facilities.
On the health and safety side, 53 percent of respondents use OHSAS 18001, and 31 percent participate in OSHA's rigorous Voluntary Protection Program (VPP).
Another common approach among respondents was to use ISO 14001 to structure their management in some facilities, but to apply similar principles to managing sites across their portfolio.
This is the case at Corning Inc., where Mark Cates, Director of Corporate Environmental Control says he instructs his team to build an engaged relationship of trust with the site-level leaders at the facilities they oversee.
"I want my guys to be considered the resource to the factories, not just a cop," he said. "Part of that is being engaged with some of the day-to-day that the factories are doing […] getting involved with what their needs are and helping them to do the right thing."
In addition to conducting frequent site visits, the EHS manager schedules monthly conference calls with the facilities leaders in the region to discuss common challenges such as interpreting new permit requirements, adapting new manufacturing processes and keeping up with ever-changing regulations.
"You get multiple factories conversing with one another, and we try to get the collaboration effect going," he said.
This focused attention on the day-to-day details is also a core component of Mr. Bopp's program as well. When it comes to permit requirements, for example, the EHS team conducts a line-by-line analysis that identifies: what type of tasks and actions are required, who is responsible and what will be done to demonstrate and verify compliance.
"The concept is to create a formal documented method of doing permit reviews so that we achieve compliance 100 percent of the time," he said.
The company also uses a suite of 'visual management' tools to help employees understand what compliance looks like. An air emissions source, for example, might be fitted with an easy-to-read gauge to demonstrate compliance with air flow requirements.
"When you continually demonstrate compliance, both visually and through routine standard work, your audits become easier and it becomes easier for the sites to demonstrate to auditors that we're doing the right thing," Mr. Bopp said.
The auditing process itself is similarly thorough and on-going. Each year the sites perform a formal self-assessment each year, which takes about six months to complete. Among the NAEM survey respondents, this internal review was likewise a common practice, with 96 percent reporting that they use internal audits to verify EHS compliance.
Depending on the size and the risk of the site, Mr. Bopp said his corporate team may also conduct an external Honeywell 'corporate' audit that combines environment, health and safety.
At Corning, audit frequency is based on risk level, too. To determine the schedule for environmental audits, Mr. Cates evaluates the risks associated with the manufacturing process, the factory location and the facility's performance on such measures as five-year average on incidents. Those in the highest-risk category will receive an annual audit, while those that have never had a controllable incident might be formally reviewed every four to five years.
For issues that arise during the environmental audit, the facilities are assigned 60 days to address the item. The company tracks corrective actions using an EHS software system, and Mr. Cates personally verifies the closure during a future site visit.
"Everything is in constant motion so regulations are changing, limits are changing," he said. "Most of the things we find are details; they're nits that we just want cleaned up."
Rebecca Corbin, Project Manager at O'Brien & Gere, who attended the NAEM conference, said she was surprised by how robust the internal audit systems are among the companies who responded to the survey.
"It seemed that most of the facilities had some sort of corrective actions follow up program to ensure that the corrective actions were addressed in a timely manner," she said. "It's reassuring to see that so many of the respondents seem to really take the audit results seriously and want to implement continuous improvement at their facilities."
Managing corrective actions, though, is just one small piece of the overall compliance assurance system for companies such as Honeywell.
"It's not really a punitive process. It's a process of continuous improvement and when you identify where the gaps are and you close those, you become better," Mr. Bopp said.
Indeed, Mr. Cates agrees the audits do more than identify corrective actions. They're an opportunity to re-think existing processes as well.
"You step back and say, 'What are some things that we see that you might get bitten by? And let's avoid that so that you can be successful in the future.'
For more information about NAEM's research please visit http://www.naem.org/?page=Research. To see more results from NAEM's benchmark of EHS management systems, please log onto: http://www.naem.org/?page=comp_2014_benchmarki.
Topics:
Health & Safety
Related
About the Author
NAEM Staff
The National Association for Environmental, Health and Safety, and Sustainability (EHS&S) Management (NAEM) empowers corporate leaders to advance environmental stewardship, create safe and healthy workplaces and promote global sustainability. As the leading business community for EHS&S decision-makers, we provide engaging forums, a curated network, peer benchmarking, research insights and tools for solving today’s corporate EHS&S management challenges. Visit us online at naem.org.