Five Strategies for Advancing EHS Compliance Excellence
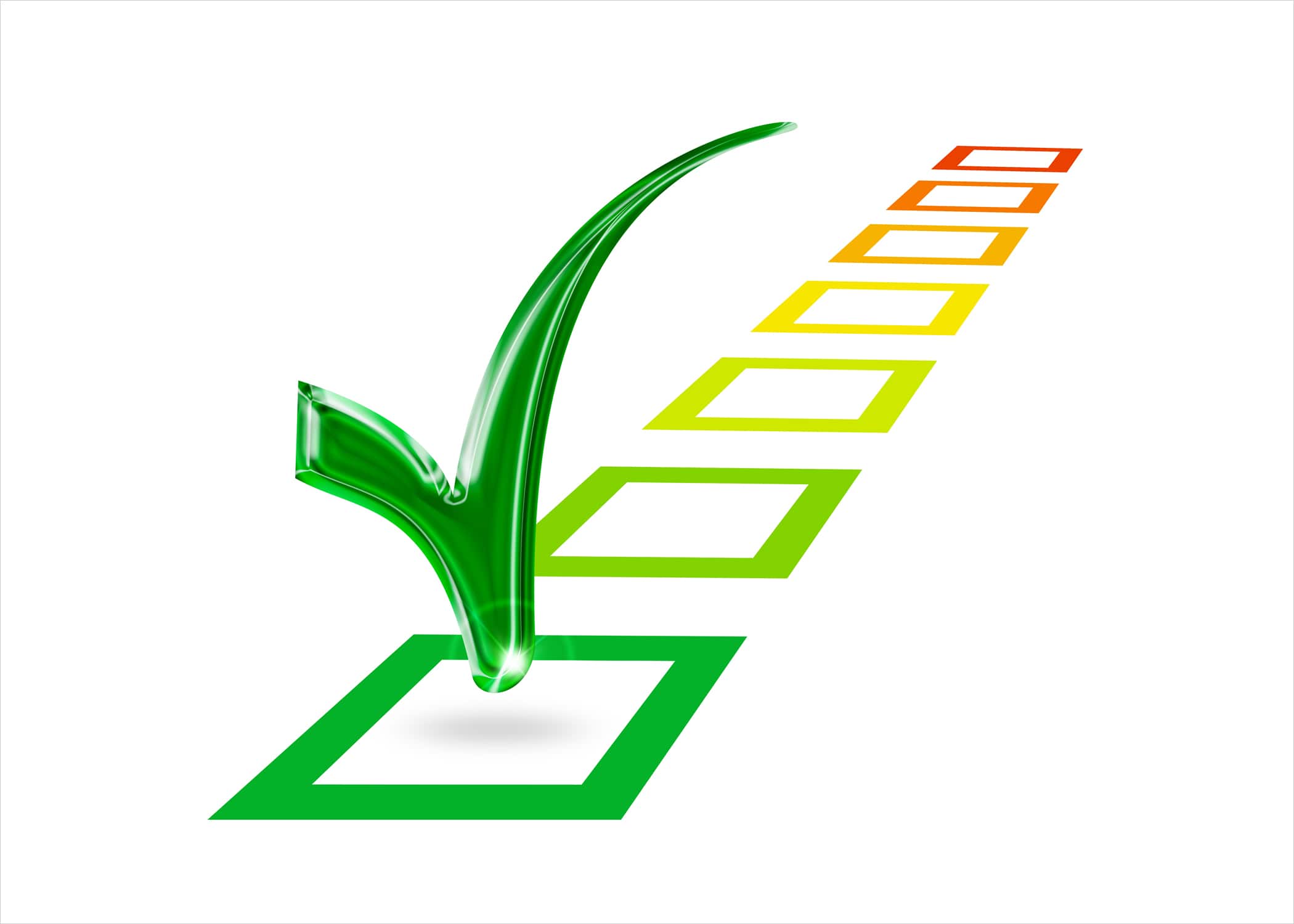
"Environmental compliance and risk management have been a very important part of our culture for a long time," said Dawn Krueger, Compliance Assurance Manager for Operations at 3M Co. "Having said that, we're never at the end game."
The path to excellence may differ for each company, but according to those who have built strong compliance systems, there are a few common strategies that seem to undergird their continued success.
#1: Clearly communicate the expectations
One of the foundational elements of a strong program is a set of clearly defined expectations.
At 3M Co. this is the work of Ms. Krueger and her corporate EHS auditing team. They are responsible for tracking regulatory changes, interpreting their applicability and implementing the changes at the facility level.
"Requirements are so complicated, it's not necessarily intuitive how to do the right thing for the environment," Ms. Krueger said.
By tracking regulations at the corporate level, she says the company can ensure consistency in how the rules are applied at its more than 100 facilities across the United States. Whenever there is a change in regulations, subject matter experts review the updates and translate them into training materials that teach employees how to comply with the revised standards.
"We don't want to leave interpretation of new regulations and implementation of new regulatory requirements to each facility," she said. "It's not just reading the rule; it's reading the guidance documents and the responses to comments, any interpretations that EPA has published for other industries."
For Mitch Mitgang, Director of Environment, Safety, Health and Security at ITT Corp., clear, focused communication is likewise at the heart of the company's compliance program.
"It's been my experience that overly large, cumbersome manuals-- what I call ‘The Plethora of Policies'--are counterproductive," he said.
To avoid this pitfall, Mr. Mitgang asked a cross-functional team to streamline ITT's EHS policies using the same ‘LEAN' approach the company uses to manage all other aspects of its operations.
"We cut out anything that was extraneous, we simplified it in plain language," Mr. Mitgang said. "It enhances communication ability, it fosters an environment where folks can understand what their accountabilities are, and it helps us to assure that they are successful at their EHS responsibilities."
And since ITT operates in more 35 countries, Mr. Mitgang says it was important for the company to ensure that its requirements were equally clear in all of the languages in which it does business. To achieve this, ITT entrusted the task to its insurance broker.
"They understand risk and insurance...who better to translate ESH technical standards?" Mr. Mitgang said. "What we got back were clearly delineated translations that actually reflect the requirements in each of the countries where we do business."
#2: Set ambitious goals
No matter where your program falls on the compliance continuum, there's always room for improvement, according to Frank Marino, Senior Corporate EHS Manager at Raytheon Co.
"Once you've achieved a very low injury rate, now you say, ‘Ok, so what do we do next?'" he said. "[It's] sort of like losing weight: ‘Ok, so I've lost 20, how do I lose the last five?'"
To spur continued compliance excellence at Raytheon, the company set an internal goal of certifying 43 of its major locations under the Occupational Safety and Health Administration's (OSHA) prestigious Voluntary Protection Program (VPP) by the end of 2013.
"Our Department of Defense customers are also pursuing VPP certifications for their operations…so it's a little bit of a competitive advantage," Mr. Marino said. "You can say that you're a ‘VPP-Star location'. That means something."
There are only 2,339 VPP-certified sites in the United States, according to OSHA, and achieving this status is not easy. Doing so requires an injury rate less than, or equal to, the Bureau of Labor Statistics standard; a rigorous application and an in-depth OSHA inspection of the facility.
"The idea is that you have to be really confident that you're in compliance with the health and safety requirements because you are, after all, inviting OSHA into your factories," Mr. Marino said.
Raytheon began pursuing its goal by conducting a gap analysis to assess the program maturity at each of its facilities. Next, it established a timeframe for bringing each site to VPP-readiness, and assigned a member of Mr. Marino's corporate team to putting the sites on the road to certification.
That pathway includes a series of internal audits, during which inspectors look for more than just the absence of egregious violations. A VPP-worthy site, Mr. Marino says, is one in which the employees are visibly committed to the overall safety culture.
"Everyone has to be totally engaged around safety in the facility," he said. "The leaders have to be talking about safety, you have to have to have some sort of safety committee going on, some active way for employees to bring issues forward."
To date, the company has already certified 30 sites—an achievement Mr. Marino says he plans to continue building upon.
"You don't get to Mount Olympus and then sit back and have a pina colada," he said. "You've got to be continuously improving."
#3: Never miss an opportunity to train
According to Ms. Kreuger, a well-trained staff is among her most important compliance assets at 3M. And auditing is one of her prime opportunities for training, she says.
"They're learning more about the requirements that they have to meet so they come away from that audit, not just with a list of action items, but with a better knowledge of what they're supposed to be doing on a day-to-day basis," she said.
The audits are also a valuable opportunity for the EHS staff to learn how their systems are working in a real-world context. During an inspection of a facility, the auditors identify issues that may need more focused attention from the corporate team.
A subject matter expert then reviews the audit results from all facilities to see if there are common challenges or misunderstandings. This analysis may result in more training, improved guidance documents or communications to other facilities in advance of their scheduled audit.
"We use the auditing program to propagate solutions across the company and really help people from reinventing the wheel," Ms. Krueger said.
3M likewise encourages employees to share common problems during conference calls, which take place every month. The calls are an open forum for environmental professionals from the facilities to discuss the issues they're concerned about, and to share best practices with one another.
This spirit of collaboration is important to the developing both the EHS staff as well as the company's overall culture, she says.
"We have to make sure that we do a really good job of requesting input from people at the facilities and other people around the globe in all of the countries where we operate," she said. "That just energizes the whole EHS team so that we can keep moving everything forward."
#4: Use software tools
While technology alone does not trump the importance of human resources, software systems are another valuable tool for driving EHS principles into your operations and creating continuity.
"The management information system is arguably just as important [as human resources] because if that one person decides to go from Xerox to Intel, so now what?" said Mr. Marino. "Does all of that institutional knowledge go with them? Or does it reside in a central, EHS management information system that somebody else can just pick up?
Technology also plays an important role in ITT's compliance program. After paring the company's EHS policies down to its fundamental components, Mr. Mitgang's team hired an external firm to create custom software tools that make it easy for employees to follow ITT's standards in their daily work.
The software program dissects the standards into core elements, which are presented as binary questions that guide employees through both the company's requirements as well as the specific country requirements. This simple presentation makes it easy for employees to definitely know whether or not they're in compliance, Mr. Mitgang says.
"It's kind of like EHS&S in a box," he said. "Everything is neatly packaged, clearly defined and very user-friendly. You do not need to be an ESH professional to maintain regulatory compliance and improvement work at ITT."
Among its innovations, the software features suite of ‘easy tools' that show employees how to reduce compliance risks in the workplace.
"We don't assume that operators of the machine are engineers, and they're going to necessarily know all of the machine guards that are needed," said Mr. Mitgang.
Instead, the software tool allows employees to click on a picture of a machine to see the list of requirements for that equipment. It also includes tools to help supervisors spot ergonomics exposures. By clicking on a picture of an employee's posture, a supervisor can pull up a list of suggestions for making the job easier.
"If an employee is reaching for a pallet at floor level to retrieve a box of parts, we would have suggestions that come up and say: ‘They should stack the pallet on top of other pallets using a forklift truck," he said.
In 2013 to-date, the software has led to the more than 300 ergonomic improvements, according to Mr. Mitgang.
The system does more than just facilitate employee awareness about safety requirements, however. The built-in corrective action tracker allows Mr. Mitgang to assign specific items to employees with a due date. As of October, he says the company had closed about 65 percent of its action items.
"It's not just that we say, ‘This is the way your machine should be guarded.' We actually make sure that they're guarded. It's not just that we say, ‘An ergonomic evaluation should be done.' An ergonomic evaluation is done," he said.
#5: Develop a strong EHS culture
The ultimate success of ITT's software system, however, is how it has strengthened the company's overall EHS culture. This is important, Mr. Mitgang says, because the EHS staff cannot personally oversee every aspect of the company's program.
"We are the coach," he said. "It's genuinely not our responsibility to carry out compliance and risk-improvement activities. It's also the front line supervisor and the employees' responsibility."
Ms. Kreuger agrees that having a strong compliance culture not only democratizes responsibility for EHS, but it allows an organization to avoid continually re-building its systems.
"It's not champion-dependent, so even when we have retirements or CEO changes, environmental compliance, risk management and pollution prevention is so much part of our company that we don't have to start over," she said.
Maintaining this strong culture requires constant engagement at all levels, she says. Beyond its regular audits, the 3M EHS team seeks regular feedback from employees to find out how they think the company is performing on EHS. She says the company pays close attention to the survey results, as a negative finding could indicate a problem—or the beginning of one.
To keep the business unit management involved, the EHS team issues quarterly scorecards with core metrics such as waste reduction, volatile organic compound (VOC) emissions reductions and audit finding results.
Demonstrating leadership involvement is an essential ingredient in Raytheon's program as well, Mr. Marino says.
"You can have a site with a very over-zealous EHS staff that's really working hard to keep all of the plates in the air but if they're doing it all by themselves and leadership is not really behind them, they're not going to be totally successful," he said.
Topics:
Compliance Excellence
Related
About the Author
NAEM Staff
The National Association for Environmental, Health and Safety, and Sustainability (EHS&S) Management (NAEM) empowers corporate leaders to advance environmental stewardship, create safe and healthy workplaces and promote global sustainability. As the leading business community for EHS&S decision-makers, we provide engaging forums, a curated network, peer benchmarking, research insights and tools for solving today’s corporate EHS&S management challenges. Visit us online at naem.org.