Five Keys to a Successful Ergonomics Process
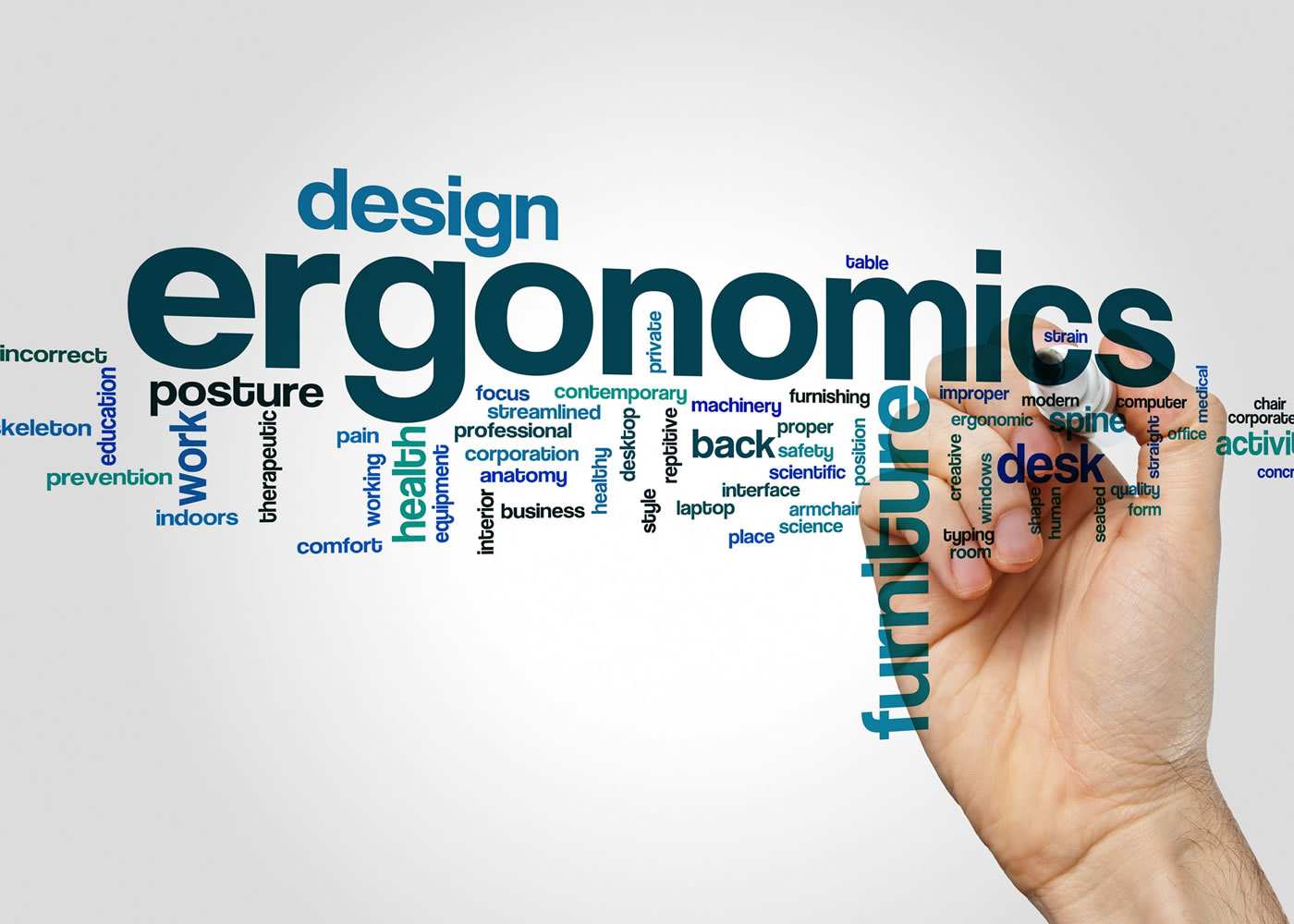
- Treat ergonomics as an engineering discipline. In doing so, the focus shifts to the design of workstations, equipment, and products rather than the treatment of employees after they are injured. It matures your program to a proactive state.
- Manage ergonomics as an improvement process. Plan-Do-Check-Act is a commonly-adopted process model across companies. Aligning your ergonomics program activities using such a model will provide a systematic approach and help synergize with other organizational initiatives.
- Establish common metrics and key performance indicators. Metrics drive ergonomic assessment and improvement activities. One such recommended metric is risk reduction - a leading indicator of results. It requires baseline assessments to identify operations with the highest risk-factor exposure, implementing improvements, and conducting follow-up assessments, all using a quantifiable tool.
- Establish a program sponsor within senior level management. The role of program sponsor is to provide long-term vision, on-going consistent support and hold people accountable.
- Leverage technology. Find the right platforms to track, report, and demonstrate results and best practices across the organization.
For those of you who have rolled out a global ergonomics program, which strategies were particularly effective? Do What are some of the lessons you've learned from the process?
To learn more about how Cardinal Health implemented a global ergonomics program, join Humantech for the NAEM webinar on "Enterprise-wide Ergonomics: Lessons Learned from a Global Implementation."
About the Author
Deepesh Desai
Deepesh Desai is the Director of Consulting for Humantech, where he oversees complex, large-scale ergonomics programs. In this role he has helped companies achieve best-in-class results by implementing workplace improvements and training programs that increase productivity, enhance product quality, and reduce injuries and illnesses. His recent client engagements include Cardinal Health, ExxonMobil, Inteva Products, Land O’Lakes, Tesla, and ZF TRW.