Focused Resources Ensure Consistency in 3M Co.'s Life cycle Assessments
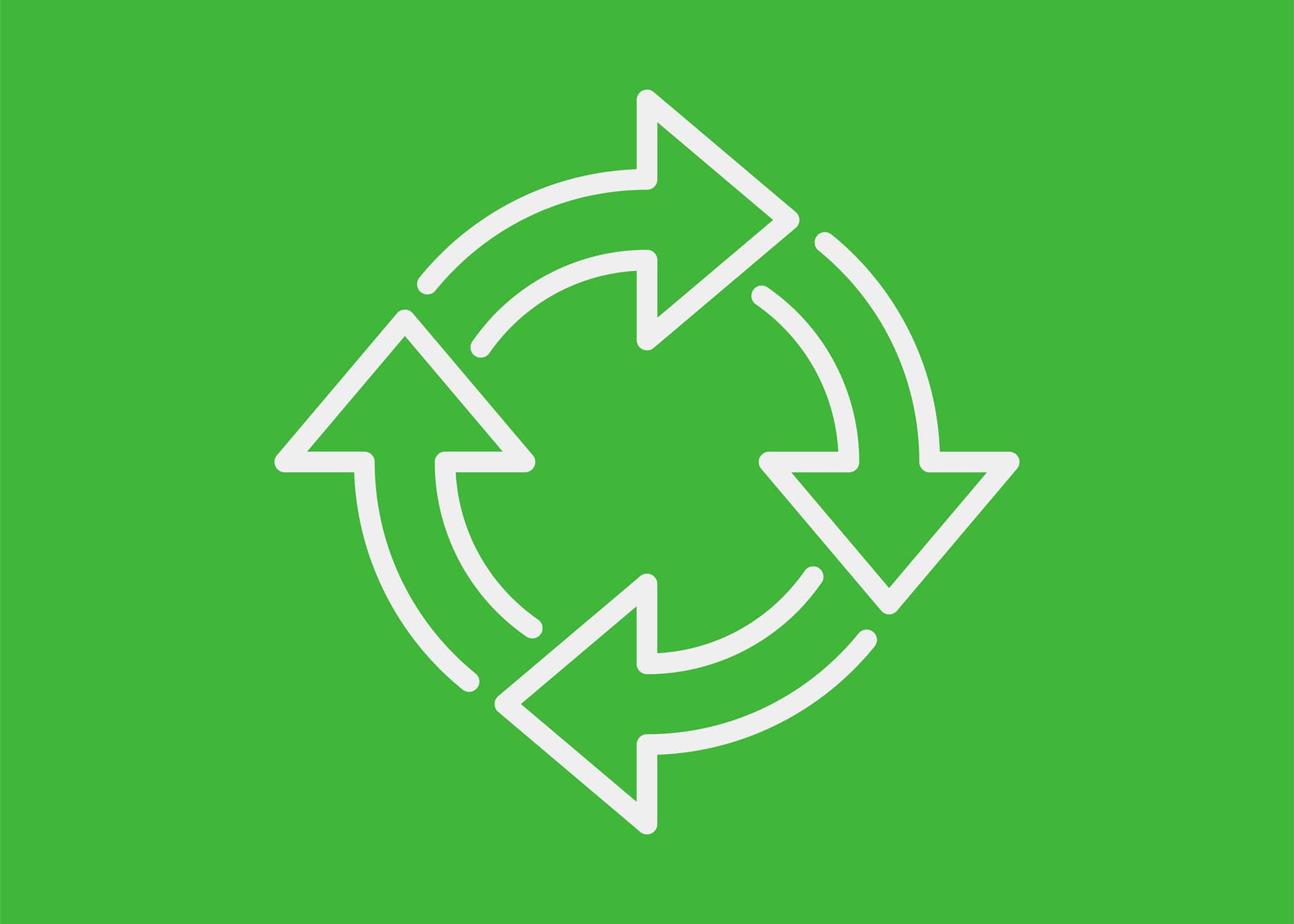
GT: How did 3M develop its standards for Life cycle assessments (LCAs)?
Stefanie Giese-Bogdan: We worked with the World Business Council for Sustainable Development (WBCSD) on developing their product carbon footprint standards. We always strive to use internationally accepted standards, so our default standards for all lifecycle assessments is ISO 14040 series. That is what we use as the default unless otherwise specified.
GT: What are the criteria for a good LCA?
SG-B: For me, LCA has three major parts to it. You need to have scientifically sound data and it needs to be consistent, so that data can be used globally. The third major part is protection of confidential information. By having a corporate group doing our LCA, we can ensure all three of those.
GT: What does 3M's process look like?
SG-B: Our LCA program is a part of 3M’s sustainability program, so it’s connected to all of our other sustainability efforts. It’s not in a vacuum. We have focused product resources for the global team here in St. Paul, but we also have team members in Europe. We don’t yet have team members in other parts of the world, but that is really because the focus has been on Europe with some of their regulatory and standards developments.
When I do a life cycle assessment on a product, we might have different technologies that are used to make that product. Quite often, we are in the situation in which a technology is export-controlled, which means that you cannot provide information about that technology outside of the United States, even within the same company. By having a corporate resource, I can create the lifecycle assessment for technologies, chemistries and product and then package it in a way that protects that confidential information, and that Europe can use to develop their product LCAs. This also leads to consistent LCAs for the product that can be used for the product across the globe.
GT: Why does the company conduct its own LCAs? Why not use a third-party?
SG-B: If I were to use independent resources in all different areas of the world, we wouldn’t have one process, we couldn’t share data, I couldn’t have built that into a library of different products or chemicals or technologies that I can use across the world because it wouldn’t be necessarily done with the same processes. Existing LCA standards are fairly vague (especially if no PCR is available) and there’s always ways to interpret them. Developing LCA internally enables consistency, sharing of data globally. In addition, we often use third-party verification for our LCA, for data that goes outside the company.
GT: How do you prioritize which products get an LCA?
SG-B: 3M is a global company with more than 60,000 unique products. If I did life cycle assessments on all of them (considering that life cycle assessments also have a limited life span), I don’t know how many people I would need in my group, but it would be orders of magnitude more than I have.
Customer demand is the biggest decision-maker for prioritization in terms of whose LCA we’re going to work on. But even within that, we might have to decide what to do. Marketing and positioning of the product is the second highest consideration, prioritized based on market share and the importance of the product to that business. It may be that it’s a developing product or a well-established product where we want to maintain our status in the market. Or, it’s a product where we’re thinking about introducing a more sustainable line of products and we want to develop a good story before we do that. Another area that is starting to grow and will likely be more important are the regulatory and the reporting requirements. Right now, in Europe, only France has a regulation where you will need an LCA for specific products to make specific claims. So it’s a very limited regulation, but it’s the first one out there. And usually that means that it’s not going to remain the only one for long. So I’m thinking that there will be more regulatory requirements developing all of the time that might even push some of the other requirements out of the way in importance. Right now, regulatory demand is not a big driver.
GT: Are there ways to improve product sustainability without conducting LCA?
SG-B: We don’t use life cycle assessment in a vacuum. We have other tools that we use for sustainability in addition to lifecycle assessment. One program many people are familiar with is our “3P - Pollution Prevention Pays” program. We also use life cycle management. Life cycle management is used during the development of all new products to manage EHS and Regulatory aspects throughout the life cycle of a product. Doing this helps avoid what life cycle assessment would identify as a hot spot (an area that you need to improve the environmental, health or safety impact categories). For life cycle management, we try to address these aspects during the product development process. Life cycle assessment normally is used once you have a product and process and modifications are a lot more difficult and costly compared to addressing these issues during product development as we do in our life cycle management program.
Topics:
Sustainability
Related
About the Author
NAEM Staff
The National Association for Environmental, Health and Safety, and Sustainability (EHS&S) Management (NAEM) empowers corporate leaders to advance environmental stewardship, create safe and healthy workplaces and promote global sustainability. As the leading business community for EHS&S decision-makers, we provide engaging forums, a curated network, peer benchmarking, research insights and tools for solving today’s corporate EHS&S management challenges. Visit us online at naem.org.