Identifying Hazards In Non-Routine Work & Emergencies
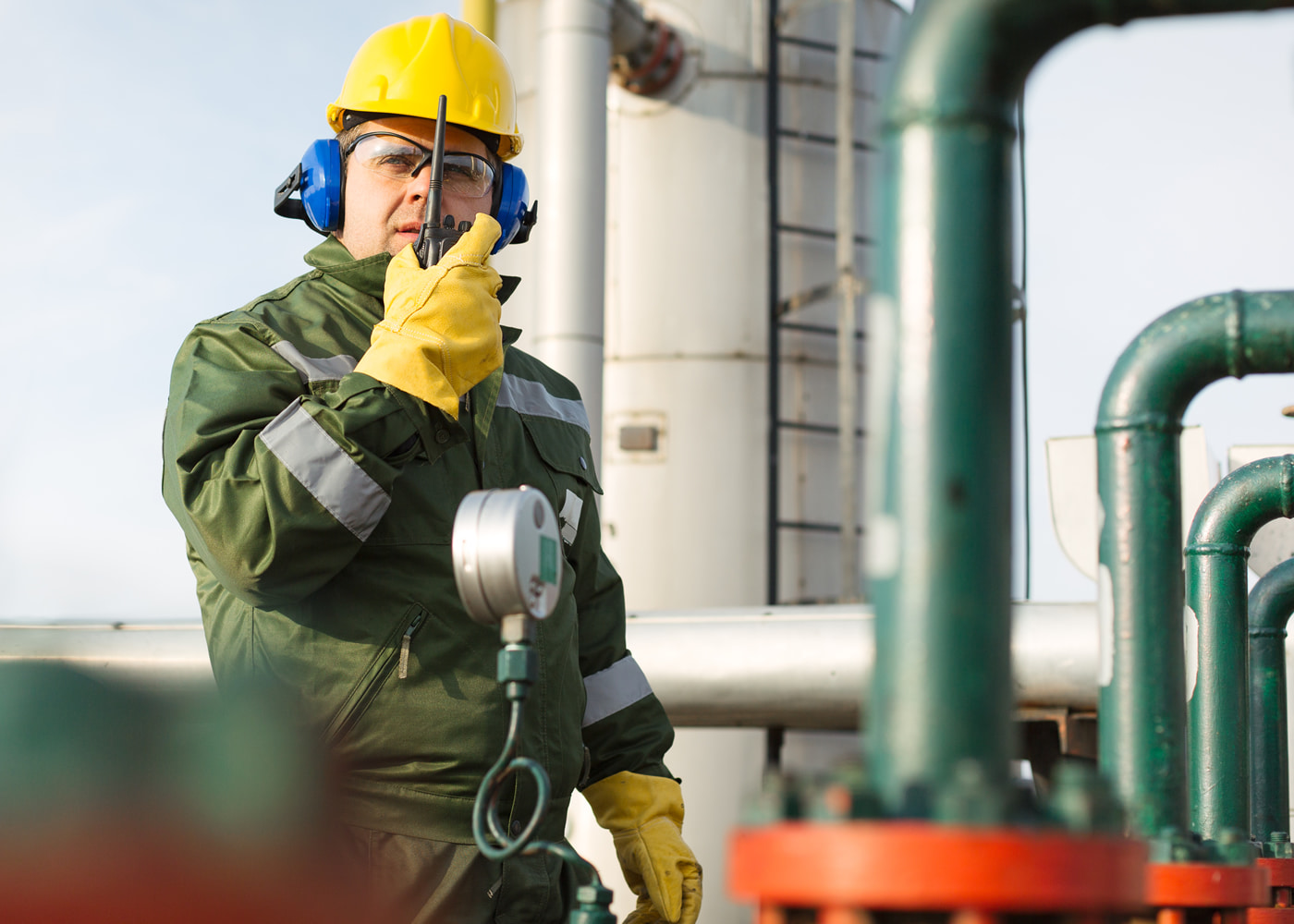
No one expects an emergency, crisis or disaster. Floods, hurricanes, tornadoes, indoor or outdoor fires (such as wildfires), toxic gas releases, chemical spills, explosions and workplace violence trigger our survival instincts. Amid chaos – potential communication breakdowns, power outages, ominous odors or smells, deafening noise, panicked coworkers, injured coworkers, debris, blocked exits, structural damage and more – life-threatening hazards are often the last thing on our minds. We want to flee, escape, get out. But emergencies and disasters can strike anyone, anytime, anywhere.
Non-routine or infrequent work also catches us by surprise. A machine suddenly fails and needs instant repair. A gasket of a pump unexpectedly must be replaced. Or perhaps it is a broken conveyor belt that needs replacement. A short circuit causes electrical wiring to be repaired quickly. Or a satellite dish on a facility roof comes loose in a windstorm and needs to be secured. These situations create immediate pressure and tension. There is a rush to repair or replace so operations can continue. Workers are nervous, anxious, because downtime can affect everything from production goals to bonuses.
Time is of the essence when non-routine work is necessary or emergencies erupt out of nowhere. Everyone feels the pressure to deal with these situations as fast as possible -- whether it is a matter of "fix it" or "flee."
Reacting Versus Responding
There is a difference between reacting and responding to non-routine work, emergency maintenance, and natural or man-made crises and disasters. We react and rely on our instincts when there is no preparedness planning, training, procedures, drills, and proactive hazard identification for foreseeable non-routine and emergency scenarios. It is likely we are not thinking about evacuation routes; slip, trip or fall risks; spills on the floor; electrical hazards; or gasoline, solvents and flammable chemicals that might explode when the flames of a fire are roaring, heat is stifling, vision obscured and the air suffocating.When we react almost spontaneously to do emergency repair work or handle an unusual, infrequent work assignment, without training, pre-planned hazard identification and procedures, we probably will not stop to consider: Is the work area clean and clear? Is the ladder secure and extended three feet above the landing? Is the machinery properly locked out? Has the confined space been evaluated? How heavy is that load I'm going to lift? Can I fit in that tight space without getting pinched, cut, or struck by pieces of equipment?
In contrast to a reaction, a response is planned. Time and resources have been allocated to ensure, as much as is feasible, preparedness. Foreseeable emergency and non-routine scenarios have been identified. Audits, walkthroughs and other visual exercises as well as data collection and review have identified hazards. The degree of risk these hazards pose have been assessed. Job hazard analyses have been conducted. Containers are labeled. Safety data sheets readily accessible. Risk assessments, emergency or task procedures, necessary tools, personal protective equipment and hazard controls have been identified, stocked and installed if necessary (in the case of controls). Employees have been trained. Procedures, responsibilities and accountabilities are put in writing, documented and communicated to everyone who needs to know. If necessary, third parties – local fire departments, law enforcement, emergency medical services and community officials – have been consulted.
Human Performance
In human performance terms, training and perhaps simulations have moved employees from knowledge-based performance mode to rule-based performance mode or skill-based performance mode.- Knowledge-based mode might better be called lack of knowledge mode. This is because we rely on knowledge-based performance when we don't know what we're doing, such as when faced with wholly unfamiliar situations (emergencies and non-routine jobs, for example). In these cases, we rely on our existing knowledge to help us – which may be shallow if we have never encountered the situation before.
- Rules-based performance occurs when a worker applies written or memorized rules to navigate an unfamiliar situation. This can apply when changes in context prevent an individual from relying on skills that have been developed (skills-based performance) or when lessons from operating in knowledge-based mode are internalized for future application.
- Skills-based performance describes situations in which workers perform a task with little conscious thought. This is usually the result of extensive experience with a given operation. When operating in a skills-based mode, individuals rely on pre-programmed,
automatic behavior.
The Need For Visual Literacy
Visual Literacy is integral to responding to emergencies or engaging in non-routine work in a disciplined and methodical approach. Employees are trained to use all their senses to make good decisions in a crisis or in unusual, infrequent work circumstances such as emergency maintenance or start ups/shutdowns. Slowing down, even a bit, to see is vitally important. About 90% of the sensory information we take in as individuals is visual. What we really see – as opposed to quick glances or observations – determines the effectiveness of our hazard identification efforts. And detailed, quality hazard identification is a core component to responding as safely and as well-prepared as possible to emergencies and non-routine work.Visual Literacy is a methodology to train people how to see. One technique of Visual Literacy uses the Elements of Art. This exercise in art education has been taught for decades to see with more clarity and understanding by examining a painting, an image, and yes, work conditions, by looking for colors, lines, shapes, space and texture.
Previously unseen hazards emerge when Visual Literacy teaches us to slow down and describe work conditions. Consciously looking at color, lines, shapes, space and texture allows us to deconstruct a work task or work area to identify where the dangers lie. Perhaps housekeeping has not lined up pallet loads with enough space in-between to maneuver. Or a loading dock has worn flooring with little traction. This in-depth "seeing" allows us to use the critical thinking skills of analysis and interpretation. Hazards are assessed for their degree of risk. Assessments lead to action plans to eliminate or mitigate those hazards. Critically, learnings and plans are communicated throughout the organization. These steps comprise the methodology of Visual Literacy.
Proactive Preparation
OSHA on its website emphasizes the need to identify "foreseeable emergency scenarios and non-routine tasks, taking into account the types of materials and equipment in use and the location within the facility." Visual Literacy is a valuable hazard identification asset to proactively prepare for predetermined emergencies and non-routine scenarios.For additional insight into COVE's Visual Literacyapproach, download the white paper "Identifying Hazards In The Workplace – A New Approach That Starts With Seeing."
Related
Sponsored Content
About the Author
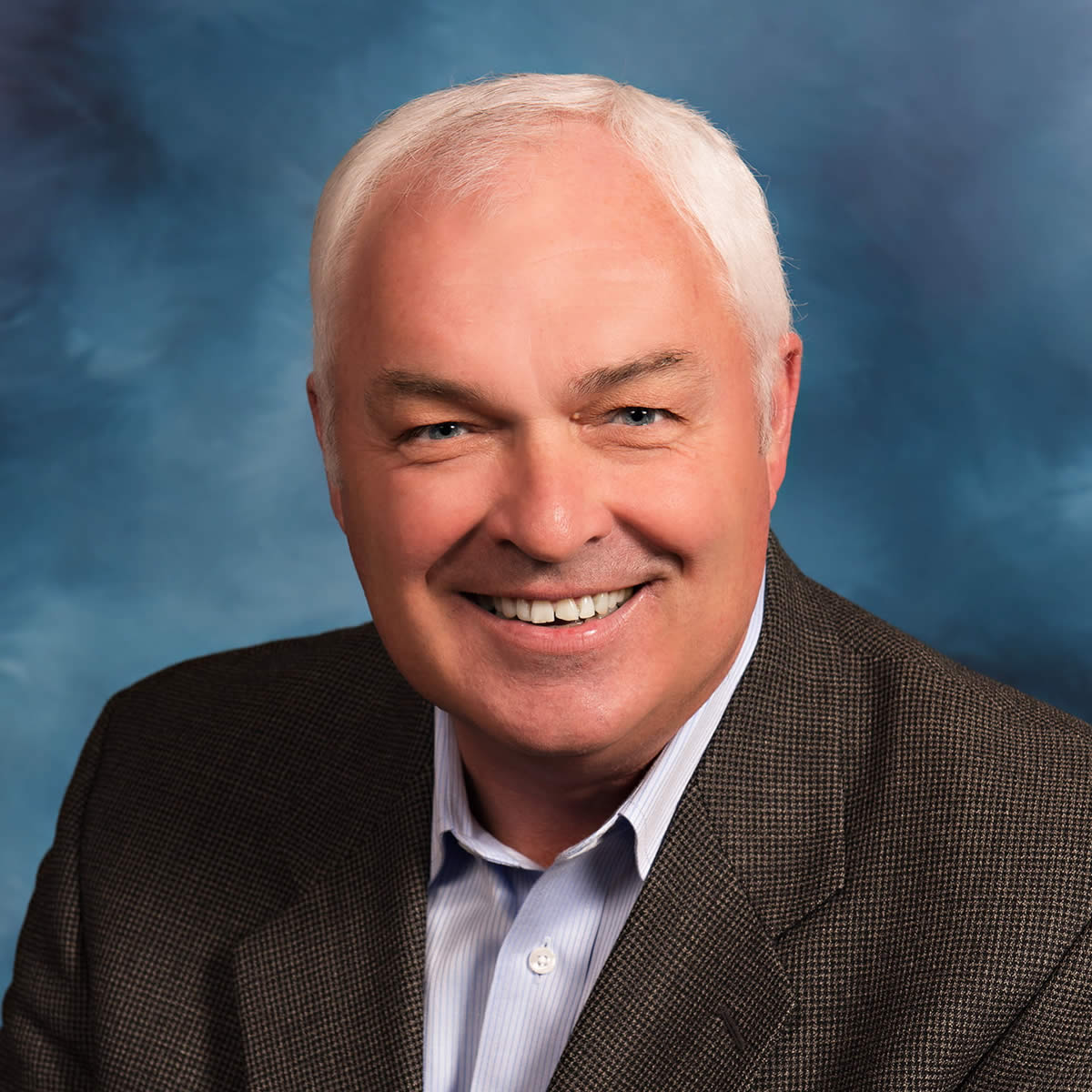
Doug Pontsler
COVE
Doug Pontsler is Chairman and Managing Director for COVE, the Center of Visual Expertise. Launched in 2018 by the Toledo Museum of Art, COVE is dedicated to the application of visual literacy for industrial and service applications with an emphasis on
safety. In this leadership role he is responsible for all aspects of the enterprise including thought leadership, product development and client satisfaction.
Prior to his current role, Doug was the former vice president of operations sustainability and EHS for Owens Corning (retired). he joined Owens Corning in 2002 and held leadership positions including director of corporate services and vice president of global sourcing. Prior to joining Owens Corning, Doug spent 23 years with Eaton Corporation. While at Eaton, he held various roles of increasing responsibilities in accounting, finance, production and inventory control management, factory management, and sourcing.
Doug served as a member of the National Safety Council (NSC) Board of Directors and as the Chairman of the Campbell Institute at the National Safety Council. He is a recipient of NSC’s 2019 Distinguished Service to Safety Award. Doug is also involved in the community as past chairman of the Regional Growth Partnership and current executive board member promoting economic development, past executive committee member of the Marathon Classic LPGA Tournament, and prior cabinet member of the United Way Campaign Committee for the Greater Toledo Area.
Doug also currently serves as member of the Independent Review Committee for JobsOhio supporting economic growth in the state. He received a bachelor of science in business administration from Miami University with a major in accounting.
Prior to his current role, Doug was the former vice president of operations sustainability and EHS for Owens Corning (retired). he joined Owens Corning in 2002 and held leadership positions including director of corporate services and vice president of global sourcing. Prior to joining Owens Corning, Doug spent 23 years with Eaton Corporation. While at Eaton, he held various roles of increasing responsibilities in accounting, finance, production and inventory control management, factory management, and sourcing.
Doug served as a member of the National Safety Council (NSC) Board of Directors and as the Chairman of the Campbell Institute at the National Safety Council. He is a recipient of NSC’s 2019 Distinguished Service to Safety Award. Doug is also involved in the community as past chairman of the Regional Growth Partnership and current executive board member promoting economic development, past executive committee member of the Marathon Classic LPGA Tournament, and prior cabinet member of the United Way Campaign Committee for the Greater Toledo Area.
Doug also currently serves as member of the Independent Review Committee for JobsOhio supporting economic growth in the state. He received a bachelor of science in business administration from Miami University with a major in accounting.